All published articles of this journal are available on ScienceDirect.
Biomethanization of Cattle Manure, Pig Manure and Poultry Manure Mixture in Co-digestion with Waste of Pineapple Fruit and Content of Chicken-Gizzard- Part I: Kinetic and Thermodynamic Modelling Studies
Abstract
Background:
The increased energy consumption from fossil fuels with its attendant gas emissions and environmental problems has provided the impetus to exploit new energy source that are renewable and environmentally-friendly.
Objective:
This work focused on the investigation and evaluation of the single or individual effects of feed-inoculum ratio, temperature, and agitation speed (i.e. operating variables) on biomethanization of the mixture of cattle manure, pig manure and poultry manure (mixed animal wastes) co-digested with pineapple fruit waste and content of chicken-gizzard (inoculum) as well as to model the kinetics of biomethanization at these different operating variables and to determine the thermodynamic properties of the biomethanization process.
Method:
The biomethanization experiments were carried out in anaerobic biodigesters at operating variables of feed/inoculums ratio that ranged from 1:1 to 3:1, temperature from 25 to 60°C, and agitation speed from 30 - 70 rpm using one factor at a time (OFAT) method. The biodigesters were incubated for 70 days retention time.
Result:
The feed/inoculum ratio, temperature and agitation speed had positive impact on cumulative biogas yield, biomethane content and start-up time of biomethanization. The cumulative biogas yield and biomethane content achieved with agitation speed of 30 to 70 rpm was respectively higher than the biogas yield and biomethane content attained without agitation. Minimum cumulative biogas yield and biomethane content was respectively obtained with feed/inoculum ratio of 1:1, temperature of 25°C and agitation speed of 70 rpm; while maximum cumulative biogas yield with its biomethane content was attained with feed/inoculum ratios of 1:3 and 3:1, temperature of 60°C and agitation speed of 30 rpm, respectively. Modified Gompertz and Exponential Rise to Maximum kinetic models fitted very well to the data and thus showed better correlation of cumulative biogas production. The thermodynamic parameters of Gibbs free energy, enthalpy, entropy change and activation energy of biomethanization were estimated and evaluated, and was found that the biomethanization process was thermodynamically feasible, spontaneous and endothermic in nature suggesting hydrogenotrophic methanogenesis pathway. The activation energy of the biomethanization process was found to be 3.324 kJ/ mol. The specific heat capacity at constant volume and constant pressure, specific internal energy and specific enthalpy of the biogas and biomethane content increased with increase in temperature.
Conclusion:
Biogas/biomethane production from the biomethanization of mixed animal wastes co-digested with fruit waste and inoculum is a feasible, viable and sustainable renewable energy option that can be simulated by kinetic models and influenced by operating variables.
1. INTRODUCTION
Biomass and their wastes, depending on their characteristics, can be converted into energy and/or fuel by combustion, gasification, co-firing with other fuels and ultimately by anaerobic digestion [1]. Anaerobic digestion converts the biological materials or biomass materials (organic matter) to biogas through the following four steps: hydrolysis, acidogenesis, acetogenesis and methanogenesis [2-5]. The process and mechanism of anaerobic digestion (biomethanization) is carried out by a consortium of micro-organisms and also the activity of biomethanization process and biogas yield depends on various factors like temperature, pH, concentration of substrate/nutrients, agitation, pre-treatment of feedstock, hydraulic retention time, total solid content, organic loading rate and the carbon: nitrogen (C/N) ratio [5, 6]. All these factors need proper monitoring and control to achieve maximum yield of biogas [7].
Anaerobic digestion mainly takes place at either mesophilic (25-40°C), or thermophilic temperatures (45-60°C) [8, 9]. Though, there have been some few studies on the effect of temperature on biogas production [10-13]. Agitation is vital to maintaining intimate contact between the bacteria and the substrate in order to encourage more active metabolism [14]. It is also useful in setting free gases that will be trapped in the substrates, and exposing fresh bacteria to fresh substrates. The most important objectives of agitation are; removal of metabolites produced by methanogens (gas), mixing of fresh substrate and bacterial population (inoculation), prevention of scum or foam formation and sedimentation, avoidance of pronounced temperature gradients within the digester (i.e. uniform heat or temperature distribution), provision of uniform bacterial population density and prevention of the formation of dead spaces that would reduce the effective digester volume [15-17]. There are different methods through which agitation or stirring/mixing can be achieved and this includes the use of mechanical agitators or mixers, pneumatic agitators/mixers, hydraulic agitators, recirculation of digesters contents or recirculation of produced biogas using recirculation pumps [18, 19]. The major factors that affect agitation/stirring are the agitation strategy, agitation intensity and duration as well as the location of the agitator or stirrer [17]. Many workers have reported on the effects of agitation/mixing on the yield of biogas and performance of anaerobic biodigesters. Some of these workers like Desai et al., Karim et al., Angelidaki, Kaparaju et al. and El-Bakhshwan et al., respectively reported the positive effect of agitation or mixing either in minimal or intermittent form on biogas production while others reported negative influence and no significant or considerable effect on biogas yield, when agitation is in the continuous form [17-26]. Hoffmann et al. further reported that continuous agitation impacted negatively on the performance of the anaerobic biodigester [25]. However, because of these conflicting or contradictory results reported in the literature on the effect of agitation/mixing on biogas yield, thus there is the need for extensive investigation on the agitation of biodigester contents.
Anaerobic co-digestion of biomass wastes has been reported to enhance and/or improve the cumulative yield of biogas than mono-digestion [27-30]. Co-digestion of animal waste with other biodegradable organic waste as co-substrate has been reported. For example, co-digestion of cattle manure with food waste, cow dung with fruit waste, food waste and vegetable waste, pig/swine manure with grass silage and grass clippings and chicken droppings/manure with Cymbopogon citratus, water hyacinth and municipal sewage sludge [28, 29, 31-36]. All the above workers made use of the animal waste in their individual form without mixing with other form of animal waste and the type of fruit waste used as co-substrate by some of these workers was not stated. Prakash and Singh have reported that co-digestion of cow dung with vegetable waste in ratio 1:1 and its co-digestion with fruit waste in ratio 2:1 respectively gave the highest biogas yield [28]. However, co-digestion of cow dung, chicken manure, and pig manure and sewage waste has been reported by Sebola et al. and they observed that ratio 1:1:1:1 gave the highest biogas yield [37].
In the start-up of biogas production in biodigesters, a balanced microbial population ratio of acetogenic bacteria and methanogenic bacteria is a requirement. This requirement of a balanced microbial population and the slow rate of methanogenic bacteria growth are the fundamental problems in biodigester start-up [38]. The slow rate of methanogenic bacteria increases the required time for an equilibrium establishment between acetogenic bacteria and methanogenic bacteria and thus results in intermediate biodegradation products accumulation (e.g. volatile fatty acid and dissolved hydrogen) [39]. The presence of excess volatile fatty acids brings about the lowering of the pH and thus inhibits the rate of methanogenic bacteria growth [38], which subsequently results in delayed start-up or biodigester failure as well as reduced/low biogas yield. Hence, to avoid these problems, the bacterial community should contain sufficient levels of methanogenic bacteria. Several studies had emphasize on the importance of inoculums in anaerobic biodigestion [40, 41]. Very few works have reported the effect of co-substrate in conjunction with the use of inoculums on biogas production yield and start-up in anaerobic biodigester using animal manure as major feedstock [5, 42]. The duration of start-up phase and biogas yield depends on the type of feedstock and inoculums. The use of chicken rumen or chicken-gizzard content and rumen fluid from slaughter house has been found to be suitable for enhancing biogas production from animal manure [5, 42]. However, in most of these studies, modeling the kinetics and determining the thermodynamic properties of biogas generation were not carried out.
These observations from the above studies informed our decision to investigate the effects of biological additives, pH and total solid content on biomethanation of animal wastes made up of the mixture of cow dung, pig dung and poultry droppings in co-digestion with fruit wastes (mango, orange and pineapple) and chicken rumen as inoculum which has been reported elsewhere [5]. It was observed from the study that co-digestion of the animal waste with pineapple fruit waste at the different pH and total solid content provided the highest biomethane yield as compared to that of mango, orange and the mixture of orange, mango and pineapple fruit wastes, respectively.
Nevertheless, more information on the effects of feed/inoculum ratio and agitation speed on biomethane/biogas yield and start-up time for biogas generation is still needed. Information on the kinetics of renewable waste biomethanization/anaerobic digestions is of paramount importance and a key factor for understanding biomethanization or methanogenesis process, measurement of biomethanization speed, design and development of efficient anaerobic digester for a renewable waste conversion. Therefore, in continuation of our previous studies, the objectives of this study are to investigate and evaluate the single or individual effects of feed-inoculum ratio, temperature, and agitation speed (using one factor at a time (OFAT) method) on biomethanization of the mixture of cattle dung, pig dung and poultry droppings (mixed animal wastes) co-digested with pineapple fruit waste and content of chicken-gizzard (inoculums) as well as to model the kinetics of biomethanization at these different operating variables and to determine the thermodynamic properties of the biomethanization process. Animal manures have been established as suitable to be used as a carrier substrate due to its high buffering capacity that regulate the optimum pH in the reactor, and the high level of nutrient, micronutrients and other trace elements that enhance optimal bacteria growth [43]. Moreover, large proportion of the agricultural sector in both developing and developed countries is involved with livestock and poultry farming which results in large quantities of animal manure and other wastes which calls for public, environmental and social concerns [44, 45].
2. MATERIALS AND METHODS
2.1. Feedstock Collection and Preparation
Animal wastes made up of cattle dung, pig dung and poultry droppings were collected from LAUTECH agricultural farm, Ogbomoso, Oyo State, Nigeria. The pineapple fruit wastes were collected from Bodija market, Ibadan, Oyo state, Nigeria. While the content of chicken-gizzard (used as inoculum) was collected from Mokola market, Ibadan, Oyo State, Nigeria. The samples collected were maintained in a refrigerator at 4°C to avoid microbial action until further use. The substrates (mixed animal wastes) and co-substrates (pineapple fruit waste and chicken inoculum) were prepared according to the method of Iyagba et al. [46]. The substrates and co-substrate were washed, sundried for twenty days; oven dried at 105°C for 24 h and then mechanically crushed using a mortar and pestle to ensure homogeneity. Table 1 shows the physical and chemical characterization of the animal wastes, pineapple fruit wastes and inoculum. The characterization was carried out according to standard methods [47, 48]. The parameter that can be used to describe the suitability of a substrate for anaerobic fermentation or digestion is the carbon-nitrogen (C/N) ratio. It has been reported that very high C/N ratio in an anaerobic digester can result in a too low nitrogen concentration for microbial growth [49] as well as result in the consumption of nitrogen by the methanogens for protein production while some leftover carbon will remain unreacted, thereby leading to low biogas generation [50]. In contrast, a low C/N ratio can lead to ammonia nitrogen accumulation which can result in the digestion process inhibition [49]. Thus, it has been reported that the optimal C/N ratio for anaerobic digestion ranges from 20 to 30:1 [49]. Table 1 shows that the C/N ratios of cattle manure, pig manure and chicken manure are lower than the required optimum while the C/N ratio of the pineapple fruit waste is higher and thus can serve as a co-substrate to improve the overall C/N ratio of the anaerobic biodigester feed ingredient. The microbial species present in the feedstock were also characterized and identified according to standard methods. The results of the characterization and micro-organisms identified in each of the feedstock waste; pineapple fruit waste, cattle manure, pig manure, and poultry manure were predominantly bacteria and they are Escherichia coli, Staphylococcus species, Salmonella species, Bacillus species, Lactobacillus species, Flavobacterium species, Methanobacterium species and Pseudomonas species. The presence of these organisms in the waste may be as a result of the type of nutrient in the waste and the physical-chemical properties of the wastes [7, 11]. The chicken-gizzard content, as inoculum and source of microorganisms’ surplus was used to improve the performance of the biodigester. The microorganisms identified in the chicken-gizzard content include, Escherichia coli, Bacillus species, Lactobacillus species, and Flavobacterium species.
Parameters (%) | Cattle Dung | Pig Dung | Poultry Dung | Pineapple Waste | Inoculum |
---|---|---|---|---|---|
Dry Matter | 91.85 | 87.79 | 88.95 | 93.26 | 85.68 |
Organic Dry Matter | 95.97 | 95.29 | 94.74 | 96.88 | 94.08 |
Nitrogena | 1.69 | 1.627 | 0.508 | 0.204 | 0.539 |
Ammonium Nitritea | 0.911 | 0.825 | 0.407 | 0.256 | 0.479 |
Phosphorousa | 0.029 | 0.038 | 0.034 | 0.042 | 0.027 |
pHa* | 6.11 | 6.49 | 6.35 | 5.03 | 6.18 |
Moisturea | 8.15 | 12.21 | 11.05 | 6.74 | 14.32 |
Crude Protein | 12.68 | 16.89 | 25.79 | 4.15 | 9.89 |
Crude Fat | 1.51 | 2.02 | 1.81 | 1.84 | 2.69 |
Carbohydrate | 25.94 | 21.88 | 23.72 | 63.81 | 8.75 |
Carbon/Nitrogen* | 17.62 | 14.58 | 9.63 | 42.80 | 17.08 |
Total Acetic Acida | 0.285 | 0.217 | 0.264 | 0.481 | 0.279 |
Crude Fibre | 38.29 | 14.85 | 0.471 | 11.64 | 1.86 |
Potassium | 0.527 | 0.392 | 0.472 | 0.725 | 0.169 |
Lignin | 16.85 | 15.31 | 17.89 | 13.28 | 1.88 |
Hemicellulose | 24.89 | 23.57 | 26.41 | 17.23 | 2.94 |
Carbona | 35.49 | 39.40 | 39.74 | 28.43 | 18.79 |
2.2. Apparatus Set-Up and Experimental Procedure
The biodigester experimental set-up for the biogas/biomethane production is as shown in Fig. (1).
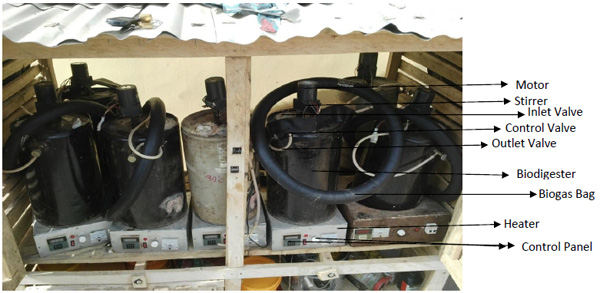
Three holes were drilled on the lid to serve as inlet valve for loading the feed, outlet valve for the collection of biogas produced and a central hole which accommodate the shaft of a stirring system (Model: RW 16 Basic I KA) with a speed range of 10 to100 rpm. Two rubber hoses was each connected to the inlet valve for injection of feed substrates and the other connected to the outlet valve through which the biogas produced will be collected into a gas bag connected to it. The rubber hose connected to the gas bag is airtight, and has a three-way valve that can be opened to collect gas samples. A digital pH meter was used to measure pH of the digested slurry and a thermocouple was used as a heating element for the digester. The digester was equipped with a control panel which permits the regulation of temperature and agitation. Efficient agitation was achieved by propeller with flat stirring paddles and four vertical baffles.
Fifteen anaerobic biodigesters labeled D1 to D15 with a working capacity of 12 kg were used. Each biodigester was operated at a given operating variable while keeping other variables constant (i.e. one variable or factor at a time). The fermentation slurry was prepared according to the composition and given amount or quantity as presented in Table (2), and then charged into the respective biodigester. The biodigesters were incubated for 70 days (i.e. 10 weeks) retention time.
Digester | Parameter | Substrate (kg) | |||||
---|---|---|---|---|---|---|---|
Cow Dung | Pig Dung | Poultry Droppings | Chicken Rumen | Pineapple Fruit Waste | Water | ||
D1 | F/I = 1:1 | 0.61 | 0.61 | 0.61 | 2.44 | 0.61 | 7.12 |
D2 | F/I = 1:2 | 0.41 | 0.41 | 0.41 | 3.25 | 0.41 | 7.12 |
D3 | F/I = 1:3 | 0.81 | 0.81 | 0.81 | 1.64 | 0.81 | 7.12 |
D4 | F/I = 2:1 | 0.31 | 0.31 | 0.31 | 3.66 | 0.31 | 7.12 |
D5 | F/I = 3:1 | 0.92 | 0.92 | 0.92 | 1.22 | 0.92 | 7.12 |
D6 | T = 25°C | 0.61 | 0.61 | 0.61 | 2.44 | 0.61 | 7.12 |
D7 | T = 30oC | 0.61 | 0.61 | 0.61 | 2.44 | 0.61 | 7.12 |
D8 | T = 40°C | 0.61 | 0.61 | 0.61 | 2.44 | 0.61 | 7.12 |
D9 | T = 50oC | 0.61 | 0.61 | 0.61 | 2.44 | 0.61 | 7.12 |
D10 | T = 60oC | 0.61 | 0.61 | 0.61 | 2.44 | 0.61 | 7.12 |
D11 | AG= 30 rpm | 0.61 | 0.61 | 0.61 | 2.44 | 0.61 | 7.12 |
D12 | AG= 40 rpm | 0.61 | 0.61 | 0.61 | 2.44 | 0.61 | 7.12 |
D13 | AG= 50 rpm | 0.61 | 0.61 | 0.61 | 2.44 | 0.61 | 7.12 |
D14 | AG= 60 rpm | 0.61 | 0.61 | 0.61 | 2.44 | 0.61 | 7.12 |
D15 | AG= 70 rpm | 0.61 | 0.61 | 0.61 | 2.44 | 0.61 | 7.12 |
Anaerobic fermentation of the slurry (made up of mixed animal wastes with pineapple fruit wastes and content of chicken-gizzard) was carried out at feed/inoculum ratio of (1:1, 1:2, 1:3, 2:1, and 3:1), temperature of (25, 30, 40, 50 and 60 °C), and agitation speed of (30, 40, 50, 60 and 70 rpm), respectively. Control experiment without agitation was also carried out. Biogas produced from the digester was collected directly into a gas bag and the biogas bag was then weighed by means of weighing scale. The mass of biogas produced was obtained from the difference between the initial mass of the biogas bag and the final mass of biogas bag plus biogas. The volume of biogas was obtained using Eq. (1):
![]() |
(1) |
Biogas yield (Y) was determined using Eq. (2) [51]:
![]() |
(2) |
2.3. Qualitative Gas Analysis
The biogas was analyzed by means of gas chromatography using the thermal conductivity detector (TCD). The equipment model is Hp6890 with HP Chem Station and Rev. A09.01 (1206) software. The carrier gas was helium at 20 ml/min flow rate with the inlet temperature of 145°C while the inflow of the carrier gas was 26 ml/min in the column with dimensions and type 30m x1/8mm x 0.85µm of and Heysep DB 100/120; Deerfield, Illinois respectively. The oven temperature was programmed at 140°C in 6 min and ramped at 50°C/min to and maintained at 175°C.
2.4. Kinetic Modelling of Biogas Generation
The biogas production kinetics for the description and evaluation of methanogenesis was carried out by fitting the experimental data of biogas production to various kinetic equations. Cumulative biogas production rates of mixed animal wastes co-digested with pineapple fruit wastes) was simulated using logistic kinetic model, exponential rise to maximum and modified Gompertz kinetic models. Logistic kinetic equation is shown in Eq. (3) [52]:
![]() |
(3) |
Where, C, cumulative biogas production (dm3/gm); k, kinetic rate constant (day-1); t = hydraulic retention time, which is the time (i.e. days) the biodigester is incubated in the course of biogas production; a , b are the constants. Exponential rise to maximum is presented in Eq. (4) [53-55]:
![]() |
(4) |
Modified Gompertz kinetic model equation (Eq. (5)) is a modified form of the Gompertz equation which is commonly used to simulate the cumulative biogas production [48]. This model assumes that cumulative biogas production is a function of hydraulic retention time. The modified Gompertz equation can be presented as follows [52, 56, 57]:
![]() |
(5) |
Where, P is the cumulative of the specific biogas production (dm3/gm), A is the biogas production potential (dm3/gm), rm is the maximum biogas production rate (dm3/gm/day), λ is the lag phase period or the minimum time required to produce biogas (day).
2.5. Thermodynamic Consideration of Biogas Generation
The thermodynamic parameters (mass fractions, specific gas constant, specific heats, ratio of the specific heats, internal energy, and enthalpy) of the biomethanization process were calculated using Eqs. (6) to (16) [58-60]. The mass fraction (ma) is estimated as given in Eq. (6):
![]() |
(6) |
The specific biogas constant (R) was estimated as given in Eq. (7):
![]() |
(7) |
Specific heat at constant pressure (Cp); specific heat at constant volume (Cv); and the ratio of the specific heats (γ), of biogas can be estimated using Eqs. (8) to (10), respectively.
![]() |
(8) |
![]() |
(9) |
![]() |
(10) |
Where for diatomic gases, Cviand Cpican be estimated using Eqs. (11) to (12), respectively.
![]() |
(11) |
and
![]() |
(12) |
While for poly atomic gases, Cvi and Cpican be estimated using Eqs. (13) to (14), respectively.
![]() |
(13) |
and
![]() |
(14) |
The specific internal energy (u) and specific enthalpy (h) of the biogas can be calculated using Eq. (15) and Eq. (16), respectively.
![]() |
(15) |
![]() |
(16) |
Where, R0 is the universal gas constant; Ri is the specific gas constant of a component gas in the biogas mixture; Mi is the mass of a component gas in the mixture; Cvi and Cpi are respectively the specific heat at constant volume and at constant pressure for component gas of the biogas mixture.
3. RESULTS AND DISCUSSION
3.1. Effect of Operating Variables on Cumulative Biogas Yield and Biomethane Content
Fig. (2) shows the effect of operating variables on the biomethanization of mixed animal wastes, co-digested with pineapple fruit waste and chicken rumen (inoculums).

The cumulative biogas yield and its biomethane content generally increased with increase in the feed/inoculum ratio (Fig. 2A) where the inoculum fraction of the ratio was increased from 1:1 to 1:2 and 1:3, respectively and as well as where the feed (substrate) fraction of the ratio was increased from 1:1 to 2:1 and 3:1, respectively for biomethanization of mixed animal wastes co-digested with pineapple fruit wastes and inoculum (content of chicken-gizzard). That is, minimum cumulative biogas yield was obtained with the feed/inoculum ratio of 1:1 and the maximum with ratio 1:3 and 3:1, respectively.
Fig. (2B) shows the effect of temperature on the cumulative biogas yield and its biomethane content. It was observed that the rate of biomethanization increased with increase in temperature. Similar observations have been reported. Manik et al. [61] obtained a maximum gas production with enriched biomethane content of 62% at 40 oC while Usman et al. reported that temperature between 30 and 60 oC influence biogas generation from lignocellulosic material [11-61]. In this study, it was observed that the digester that was subjected to a temperature of 60oC had the highest biomethane yield of 66.8% with a cumulative biogas yield of 6.8149 dm3/gm of slurry. This was relatively followed by that obtained at 50 oC (63.1%; 6.5678 dm3/gm of slurry), 40 oC (60.4%; 6.2853 dm3/gm of slurry), 30 oC (59.2%; 5.2754 dm3/gm of slurry), and 25 oC (50.1%; 3.5311dm3/gm of slurry), respectively. The increase in biogas yield and biomethane content in the biogas is due to higher digestion rate and improved solids settling [62, 63]. According to Parker, there are two temperature ranges required 25- 40°C for mesophilic and 45-60°C for thermophilic methane production; thus, the observation of higher biogas yield and biomethane content at 50 and 60 oC in this present study suggests that there are consortium of both mesophilic and thermophilic micro-organisms present in the substrates [64]. Methanogens are the bacteria that help decompose the substrate in the mesophilic temperature range, however, they become inactive at extremely high and low temperatures. Usman et al. have reported that stable reactor performance can be obtained at 55 oC and 65 oC, respectively [11]. Adeniran et al. [51] obtained a biogas yield of 26.86 ml/kg of slurry (equivalent to 0.00003 dm3/gm) in the anaerobic digestion of poultry wastes and cow dung at 37oC [51]. While Okuo et al. obtained a cumulative biogas yield of 487.5 cm3/kg (equivalent to 4.875 ×10-4 dm3/gm), 467.5 cm3/kg (equivalent to 4.675 ×10-4 dm3/gm) and 457.5 cm3/kg (equivalent to 4.575 ×10-4 dm3/gm) in the anaerobic digestion of the mixture of cattle manure, swine manure and poultry manure in the ratio 4:1:3, 2:1:1 and 4:3:1, respectively, at temperature range of
The effect of agitation speed on the cumulative biogas yield and its biomethane content is shown in Fig. (2C). It was observed that the rate of biomethanization of mixed animal wastes co-digested with pineapple fruit waste and inoculums decreased with increase in agitation speed from 30 to 70 rpm. The digester subjected to 30 rpm agitation speed had the highest biogas yield (6.2853 dm3/gm) with biomethane content (58%) and relatively followed by that of 40, 50, 60, and 70 rpm with corresponding biogas yield of 6.0028, 5.7203, 5.4379 and 5.0443 dm3/gm of slurry and biomethane content of 57.1%, 55%, 50% and 48%, respectively. The power supplied by agitation was estimated using Eqs. (17) and (18) and the result is as shown in Fig. (2D).
![]() |
(17) |
Where Np is power number and is a function of the Reynolds number (NRe) [i.e. Np= f (NRe)]
![]() |
(18) |
ρ is density of fermentation slurry, N is rotational speed of impeller, μ is viscosity of fermentation slurry, D is impeller diameter and Vs is volume of fermentation slurry, respectively.
Fig. (2D) shows that as the agitation speed increases so does the power supplied or consumed per volume of slurry/waste also increases and the cumulative biogas yield relatively decreased. Nevertheless, the cumulative biogas yield with its biomethane content obtained from the biomethanization process with agitation (30 – 70 rpm) was found to be relatively higher than the cumulative biogas yield of 4.7882 dm3/gm of slurry with biomethane content of 46% that was respectively obtained without agitation. Thus, with agitation speed of 30 – 70 rpm, increase in the cumulative biogas yield ranged from 5.3 to 31.3% and its biomethane content from 4.3 to 26.1% above the cumulative biogas yield and biomethane content obtained without agitation. According to Muthanna et al., biogas production will increase by 15% for mixed digester compared to an unmixed one [65]. Karima et al. in their study have observed an increase of 10 to 30% in biogas production with agitation [24]. Kaparaju et al. have also reported that an increase of 7% in biogas yield was attained with intermittent mixing as compared to continuous mixing [22]. Thus, a moderately agitated digester is required for optimal gas production.
3.2. Effect of Operating Variables on Start-Up Time of Biogas/Biomethane Generation
Fig. (3) shows the effect of operating variables on the start-up time of the biomethanization process of cattle manure, pig manure and chicken manure mixture co-digested with pineapple fruit waste and content of chicken-gizzard (inoculums).
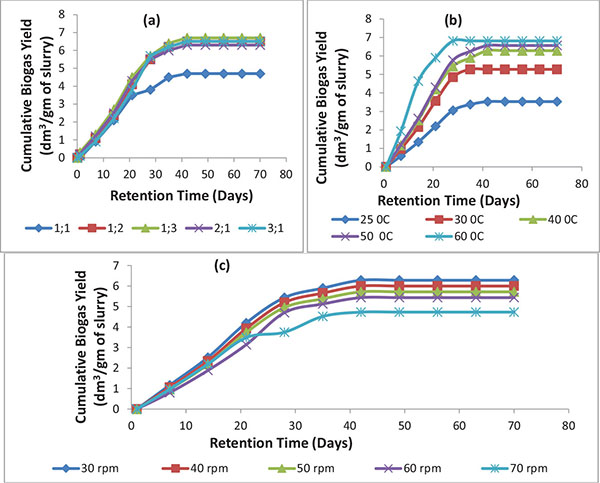
The biomethanization process started with the generation of biogas/biomethane on day 5 without the use of inoculum while it started on day 1 with the production of biogas/biomethane for the use of feed/inoculum ratio of 1:1, 1:2, 1:3, 2:1 and 3:1 and the biogas production increased until it reached its peak on day 42 (6th week) and remained constant till day 70 (10th week) (Fig. 3A).
The effect of temperature on start-up time is shown in Fig. (3B). The biomethanization process started with biogas/biomethane production on day 5 for temperature of 25oC (ambient temperature) while biogas/biomethane generation started on day 1 for temperature of 30 oC, 40 oC, 50 oC, and 60 oC, respectively. The set up at 25 oC displayed the least production rate with peak biogas accumulation yield obtained on day 49 (7th week) and remained constant till day 70. It is observed that the biodigester set up at 60 oC has the fastest production rate as it attains peak performance on day 28 (4th week) and remained constant till day 70 (10th week). This is relatively followed by biodigester set up at 50 oC, 40 oC and 30 oC, each with peak biogas accumulation yield obtained on day 35 (5th week) and remained constant till day 70 (10th week). A similar observation has been reported by Manjula et al. stating that maximum biogas production rate occurred at about 25 days for all the three cases of temperature (55 oC, 45 oC and 35 oC) that was investigated [12]. From this study, it is obvious that maximum biogas production was enhanced by the thermophilic methanogenic bacteria at 60 oC, 50 oC and 40 oC while at 25 oC; the action of the methanogenic bacteria was less effective.
Fig. (3C) shows the effect of agitation speed on start-up time. The biomethanization process without agitation started biogas/biomethane generation on day 5 while it started biogas/biomethane production on day 1 for agitation speed of 30 rpm, 40 rpm, 50 rpm, 60 rpm, and 70 rpm, respectively. It is observed that the biodigester set up at 30 rpm has the fastest production rate as it attained peak performance on day 35 (5th week) and this remained constant till day 70 (10th week). While the digester set up at 40 rpm has the second fastest production rate with peak accumulation yield on day 35 (5th week) and remained constant till day 70. This is relatively followed by the biodigester set up at 50 rpm, 60 rpm and 70 rpm which had their biogas peak accumulation yield on day 49 (7th week,), 56 (8th week) and 49 (7th week), respectively, and remained constant till day 70.
3.3. Kinetics of Mixed Animal Wastes Biomethanization Process
The kinetics of biogas production from biomethanization of mixed animal wastes co-digested with pineapple fruit wastes and inoculum (chicken rumen) was carried out by fitting the biogas production experimental data obtained at different operating parameters of feed/inoculums ratio, temperature and agitation speed to three forms of kinetic model equations which are logistic kinetic model, exponential rise to maximum and modified Gompertz kinetic model using the non-linear regression tool of MATLAB 7.0 software package and the estimated kinetic parameters and coefficient of determinations (R2) obtained are presented in Tables 3 to 5 respectively.
Models | Constant Variables | Feed/Inoculum Ratio | ||||
---|---|---|---|---|---|---|
1:1 | 1:2 | 1:3 | 2:1 | 3:1 | ||
Logistic Kinetic | a | 3.858 | 5.216 | 5.396 | 5.181 | 5.205 |
b | -3.858 | -5.216 | -5.396 | -5.181 | -5.205 | |
k(day-1) | 10.26 | 9.814 | 9.74 | 9.827 | 9.818 | |
R2 | 0.4665 | 0.4155 | 0.4427 | 0.4443 | 0.3884 | |
Exponential Rise to Maximum | A(dm3/gm) | 5.156 | 7.292 | 7.556 | 7.063 | 7.385 |
k(day-1) | 0.04223 | 0.04492 | 0.04731 | 0.03857 | 0.04443 | |
R2 | 0.9767 | 0.959 | 0.9714 | 0.9702 | 0.9517 | |
Modified Gompertz Kinetic | A(dm3/gm) | 4.798 | 6.161 | 6.844 | 6.05 | 6.233 |
rm(dm3/gm/day) | 0.02682 | 0.9342 | 27.5 | 0.02417 | 0.03591 | |
λ(day) | 1.485 | 0.9813 | 0.5067 | 0.5011 | 0.4918 | |
R2 | 0.9937 | 0.964 | 0.9936 | 0.9708 | 0.9568 |
Models | Constant Variables | Temperature(ºC) | ||||
---|---|---|---|---|---|---|
25 | 30 | 40 | 50 | 60 | ||
Logistic Model | a | 2.823 | 4.506 | 5.065 | 5.301 | 5.572 |
b | -2.823 | -4.506 | -5.065 | -5.301 | -5.572 | |
k(day-1) | 10.48 | 10.07 | 9.872 | 9.779 | 9.665 | |
R2 | 0.4101 | 0.4135 | 0.4317 | 0.4282 | 0.4458 | |
Exponential Rise to Maximum | A(dm3/gm) | 3.996 | 6.387 | 7.002 | 7.331 | 7.519 |
k(day-1) | 0.04087 | 0.04069 | 0.04333 | 0.04334 | 0.04628 | |
R2 | 0.9598 | 0.964 | 0.9676 | 0.9643 | 0.9652 | |
Modified Gompartz Kinetic | A(dm3/gm) | 3.589 | 5.39 | 5.978 | 6.299 | 6.88 |
rm(dm3/gm/day) | 47.02 | 73.54 | 164.6 | 203.5 | 205.7 | |
λ(day) | 0.5573 | 0.4994 | 0.4832 | 0.47 | 0.4412 | |
R2 | 0.9837 | 0.9692 | 0.9713 | 0.9722 | 0.9819 |
Models | Constant Variables | Agitation (rpm) | ||||
---|---|---|---|---|---|---|
30 | 40 | 50 | 60 | 70 | ||
Logistic Kinetic | a | 5.065 | 4.819 | 4.582 | 4.285 | 3.858 |
b | -5.065 | -4.819 | -4.582 | -4.285 | -3.858 | |
k(day-1) | 9.872 | 9.963 | 10.05 | 10.14 | 10.26 | |
R2 | 0.4317 | 0.4218 | 0.4155 | 0.3842 | 0.4665 | |
Exponential Rise to Maximum | A(dm3/gm) | 7.002 | 6.732 | 6.437 | 6.293 | 5.156 |
k(day-1) | 0.04731 | 0.04333 | 0.04222 | 0.04167 | 0.03748 | |
R2 | 0.9767 | 0.9676 | 0.9644 | 0.9621 | 0.9519 | |
Modified Gompartz Kinetic | A(dm3/gm) | 5.978 | 5.724 | 5.451 | 5.12 | 4.798 |
rm(dm3/gm/day) | 152.7 | 60.58 | 30.95 | 16.9 | 0.9342 | |
λ(day) | 0.4641 | 0.4755 | 0.4832 | 0.4843 | 1.485 | |
R2 | 0.9713 | 0.9699 | 0.9682 | 0.9524 | 0.9937 |
As presented in Tables (3 to 5), the R2 is relatively higher for modified Gompertz kinetic model (0.9568-0.9937); (0.9713-0.9837) and (0.9524-0.9937) as well as for exponential rise to maximum (0.959-0.9767); (0.9598-0.9676) and (0.9519-0.9767) as compared to that of the logistic kinetic model (0.3884-0.4665); (0.4101-0.4458) and (0.3842-0.4665) at different feed/inoculums ratio, temperature and agitation speed, respectively. The higher value of R2 above 0.90 for both modified Gompertz and exponential rise to maximum kinetic models indicates that both models fitted very well to the experimental biomethanization data and thus can be used to simulate biogas production from biomethanization of mixed animal wastes co-digested with pineapple fruit wastes at different condition of feed/inoculums ratio, temperature and agitation, respectively. As it could be seen in Tables (3 to 5), the kinetic constants of exponential rise to maximum, i.e. the first order kinetic constant (k) and the cumulative biogas production (A) increased with increase in the feed/inoculum ratio where the inoculum fraction of the ratio was increased (1:1, 1:2, 1:3) and where the feed (substrate) fraction of the ratio was increased (1:1, 2:1, 3:1), respectively (Table 3).
In addition, these constants i.e. the first order kinetic constant (k) and the cumulative biogas production (A) generally increased with increase in temperature and decreased with increase in agitation speed Tables (4 and 5). Similarly, for modified Gompertz equation, biogas production potential (A) and biogas production rate (rm) generally increased with increase in the feed/inoculum ratio where the inoculum fraction of the ratio was increased (1:1, 1:2, 1:3) and where the feed (substrate) fraction of the ratio was increased (1:1, 2:1, 3:1) respectively, while the lag phase (λ) decreased with increase in the feed/inoculum ratio where the inoculum fraction of the ratio was increased (1:1, 1:2, 1:3) and where the feed (substrate) fraction of the ratio was increased (1:1, 2:1, 3:1), respectively (Table 3).
Furthermore, the biogas production potential (A) and biogas production rate (rm) also generally increased with increase in temperature and decreased with increase in agitation speed, respectively while the lag phase (λ generally decreased with increase in temperature and increased with increase in agitation speed, respectively (Tables 4 and 5). In logistic kinetic model, the kinetic rate constant was found to increase with increase in feed/inoculums ratio up to 2:1 and decreased at feed/inoculums ratio 3:1 (Table 3). Also, the logistic kinetic rate constant decreased with increase in temperature as well as increased with increase in agitation speed (Tables 4 and 5).
3.4. Estimation of Thermodynamic Parameters and Activation Energy
The chromatographic analysis of biogas obtained from the biomethanization of cattle manure, pig manure and chicken manure mixture co-digested with pineapple fruit waste and content of chicken-gizzard at different temperature of 25, 30, 40, 50 and 60 oC indicated that the gas constituents are CH4, CO2, H2S, CO and NH3. Using Eq. (6) to Eq. (16), the estimated mass fractions of the biogas constituents, gas constant, specific heat capacities and ratio of the specific heats of the biogas produced at different temperature of 25, 30, 40, 50 and 60 oC, from the biomethanization of cattle manure, pig manure and chicken manure mixture co-digested with pineapple fruit waste and content of chicken-gizzard are presented in Table 6.
Temperature | Constituent | Composition % |
Mass in Mixture (kg) |
Mass fraction | Ri(kJ/kgK) | CVi(kJ/kgK) |
CPi (kJ/kgK) |
---|---|---|---|---|---|---|---|
25 oC | CH4 | 50.277 | 8.044 | 0.2743 | 0.1426 | 0.4276 | 0.5702 |
CO2 | 46.293 | 20.369 | 0.6947 | 0.1313 | 0.3937 | 0.5250 | |
H2S | 1.165 | 0.396 | 0.0135 | 0.0033 | 0.0099 | 0.0132 | |
CO | 1.159 | 0.324 | 0.0111 | 0.0033 | 0.0080 | 0.0115 | |
NH3 | 1.106 | 0.188 | 0.0064 | 0.0031 | 0.0094 | 0.0125 | |
Total | 100 | 29.321 | 1 | 0.2836 | 0.8489 | 1.1324 | |
30 oC | CH4 | 59.277 | 9.484 | 0.3470 | 0.1803 | 0.5409 | 0.7213 |
CO2 | 40.293 | 17.729 | 0.6487 | 0.1226 | 0.3677 | 0.4903 | |
H2S | 0.165 | 0.056 | 0.0021 | 0.0005 | 0.0015 | 0.0020 | |
CO | 0.159 | 0.044 | 0.0016 | 0.0005 | 0.0012 | 0.0017 | |
NH3 | 0.106 | 0.018 | 0.0007 | 0.0003 | 0.0010 | 0.0013 | |
Total | 100 | 27.331 | 1 | 0.3042 | 0.9123 | 1.2166 | |
40 oC | CH4 | 60.435 | 9.670 | 0.3617 | 0.1879 | 0.5638 | 0.7517 |
CO2 | 37.469 | 16.487 | 0.6166 | 0.1165 | 0.3495 | 0.4661 | |
H2S | 0.949 | 0.323 | 0.0121 | 0.0030 | 0.0089 | 0.0118 | |
CO | 0.574 | 0.161 | 0.0060 | 0.0018 | 0.0045 | 0.0062 | |
NH3 | 0.573 | 0.097 | 0.0036 | 0.0018 | 0.0053 | 0.0071 | |
Total | 100 | 26.738 | 1 | 0.3110 | 0.9320 | 1.2429 | |
50 oC 60 oC |
CH4 | 63.146 | 10.103 | 0.3903 | 0.2028 | 0.6084 | 0.8112 |
CO2 | 34.495 | 15.178 | 0.5863 | 0.1108 | 0.3324 | 0.4432 | |
H2S | 0.719 | 0.245 | 0.0094 | 0.0023 | 0.0069 | 0.0092 | |
CO | 0.739 | 0.207 | 0.0080 | 0.0024 | 0.0059 | 0.0083 | |
NH3 | 0.901 | 0.153 | 0.0059 | 0.0029 | 0.0087 | 0.0116 | |
Total | 100 | 25.886 | 1 | 0.3212 | 0.9623 | 1.2835 | |
CH4 | 66.817 | 10.691 | 0.4313 | 0.2241 | 0.6723 | 0.8964 | |
CO2 | 30.380 | 13.367 | 0.5392 | 0.1019 | 0.3057 | 0.4076 | |
H2S | 0.928 | 0.315 | 0.0127 | 0.0031 | 0.0093 | 0.0124 | |
CO | 0.884 | 0.248 | 0.0100 | 0.0030 | 0.0074 | 0.0104 | |
NH3 | 0.991 | 0.168 | 0.0068 | 0.0033 | 0.0100 | 0.0133 | |
Total | 100 | 24.789 | 1 | 0.3354 | 1.0047 | 1.3401 |
As presented in Table (6), it could be seen that the CH4 has the highest molar composition at various temperatures which is an indication of the high quality of the biogas produced. It also has the highest specific heat at constant volume and pressure at various temperatures. These specific heats increased with increasing temperature which is a confirmation of their temperature dependency. A similar observation has been reported for biogas generation from cattle dung by Yaru et al. [59]. The other components of biogas produced in their decreasing order of molar composition are CO2, H2S, CO and NH3. The heat capacities of these components followed the same trend as CH4. An important constant in the estimation of heat capacities of gases is the ratio of specific heat at constant pressure to constant volume (γ). All the components of the biogas produced except for CO are polyatomic gases with the value of γ being 1.33 (for polyatomic gas) while CO has 1.44 (for diatomic gas). The value of γ for the biogas is also 1.33 which is a reflection that the biogas is predominantly composed of polyatomic gases and this is in agreement with the observation and report of Yaru et al. and Eastop and McConkey [59, 66].
The specific internal energy (u) and enthalpy (h) of biogas and biomethane content obtained from biomethanization of cattle manure, pig manure and chicken manure mixture co-digested with pineapple fruit waste and content of chicken-gizzard at different temperature was calculated based on Eq. (15) and Eq. (16), respectively, and the results are presented in Fig. (4A). Fig. (4A) shows the plot of specific internal energy of biogas and specific internal energy of biomethane content against temperature (K).
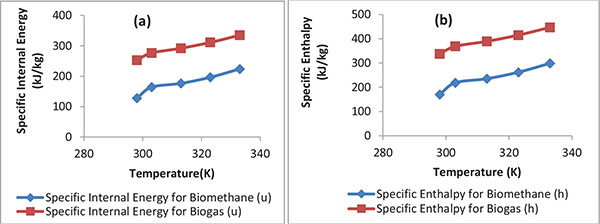
As seen in Fig. (4A), the value of specific internal energy of biogas and specific internal energy content of biomethane respectively increased as temperature increased. A similar observation has been reported [59]. The maximum specific internal energy of biomethane (CH4) content obtained is 223.8712 kJ/kg and the lowest, 127.4457 kJ/kg while the maximum specific internal energy of biogas is 335.0503 kJ/kg and the lowest being 252.9978 kJ/kg. Yaru et al. obtained 279.48923 kJ/kg and 273.95479kJ/kg as the maximum specific internal energy and the lowest specific internal energy of biogas from cattle dung, respectively [59].
Fig. (4B) shows the plot of specific enthalpy of biogas and biomethane content against temperature (K). As shown in Fig. (4B), the values of specific enthalpy of biogas and specific enthalpy of biomethane content respectively increased with increased temperature. The maximum specific enthalpy of biomethane (CH4) content is 298.4948 kJ/kg and the minimum is 169.9274 kJ/kg while the highest specific enthalpy of biogas is 446.7335kJ/kg and the lowest being 337.4935 kJ/kg. Yaru et al. obtained 375 kJ/kg as the maximum specific enthalpy of biogas obtained from cattle dung anaerobic digestion [59]. In comparison with the values obtained by Yaru et al., this study revealed that the biogas produced from the biomethanization of cattle manure, pig manure and chicken manure mixture in co-digestion with waste of pineapple fruit and content of chicken-gizzard possess higher values of specific internal energy and specific enthalpy than biogas generated from mono-anaerobic digestion of cattle manure (or substrate) [59].
In order to study the feasibility of the biomethanization process, thermodynamic parameters such as changes in standard Gibb’s free energy (ΔG0 ), standard enthalpy (ΔH0 ), and standard entropy (ΔS0 ). can be estimated. The standard Gibb’s free energy (ΔG0 ) was calculated according to Eyring-Polanyi equation (Eq. (19)) [67]:
![]() |
(19) |
![]() |
(20) |
Taking natural logarithm of Eq. (19) and substituting Eq. (20) into Eq. (19) gives:
![]() |
(21) |
Where k is the rate constant (s-1), T is the absolute temperature (K), R, kb and h are the universal gas (8.314 J mol-1 K-1), Boltzmann (1.38 x 10-23 J/K) and Planck’s (6.63x 10-34 J s) constants, respectively. The transmission coefficient κ is often taken as unity. From the plot of ln (k/T) vs. 1/T (Fig. 5),
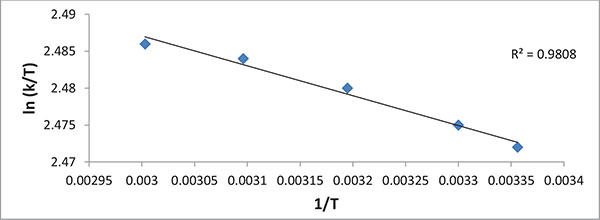
ΔH0 and Δ S0 were obtained from values of the slope and intercept, respectively, and thus Δ G0 was obtained using Eq. (20). The results are presented in (Table 7).
Temperature (K) |
Δ H0 (kJ/mol) |
Δ S0 (J/mol. K) |
Δ G0 (J/mol) |
---|---|---|---|
298 303 313 323 333 |
336.43 | 15.58 | -4306.41 -4720.74. -4876.54 -5032.34 -5188.14 |
As presented in Table 7, the positive value of Δ H0 indicates that the biomethanization process is endothermic in nature. The positive value of Δ S0 revealed that the biomethanization process is entropy driven. The negative value of H0 Δ G0 depicts that the biomethanization reaction is feasible and spontaneous. The positive value of Δ H0 in this present study implies that the biomethanization process made use of heat energy from the surrounding environment and also suggests that acetoclastic methanogens may not be the predominant microorganisms in the biodigester as these methanogens function optimally at mesophilic temperature. Krakat et al. in their studies observed that methane generation from energy crops at a higher temperature of 60°C resulted in dominance of hydrogenotrophic Methanobacteriales as compared to acetoclastic methanogens among the microbial communities with a corresponding increase in methane production in thermophilic biogas fermentor [68]. These workers reported that their observation contradicts the common anaerobic digestion model 1 (ADM1) which states that two-thirds of methane is obtained from the acetoclastic methanogens and one-third from hydrogenotrophic methanogens [69]. The negative value of (ΔG0 and the positive value of (ΔH0 ) obtained for the biomethanization process in this study would suggest in accordance with the observation of Krakat et al. that at higher temperature or thermophilic temperature (50 - 60°C) the forward reaction was highly favoured (i.e. increased product formation, in this case, biomethane) as well as the predominance of hydrogenotrophs in the biodigester which perhaps could mostly be responsible for the biomethane generation through the hydrogenotrophic methanogenesis pathway than through the acetoclastic methanogenesis pathway [68].
The activation energy of biogas production from the biomethanization of mixed animal wastes co-digested with pineapple fruit waste and inoculum at different temperature was obtained from the application of Arrhenius form of equation (Eq. (22)).
![]() |
(22) |
Where, A and Ea are the Arrhenius parameters which stand for frequency factor or pre-exponential coefficient (min-1) and activation energy (J/mol), respectively. k, is the rate constant (min-1), R is the molar universal gas constant (8.314 J mol-1 K-1) and T is the absolute temperature (K). By taking the natural logarithm, Eq. (22) can be expressed as:
![]() |
(23) |
The activation energy (Ea) was obtained from the plot of ln k against 1/T as shown in Fig. (6).
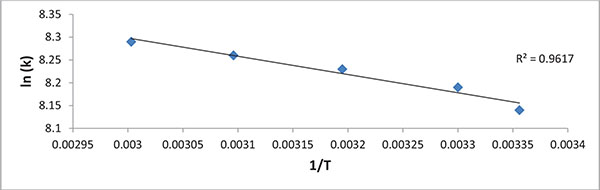
The activation energy was estimated to be 3.324 kJ/mol. The positive value of Ea that the biomethanization process is endothermic in nature and thus favoured by moderate to high temperature.
CONCLUSION
It can be concluded that cumulative biogas yield with its biomethane content obtained from the biomethanization of cattle manure, pig manure and chicken manure mixture co-digested with pineapple fruit waste (co-substrates) and content of chicken-gizzard (as inoculums), can generally be influenced positively or negatively by variation in the values or amount of feed/inoculum ratio, temperature and agitation speed. The cumulative biogas yield and its biomethane content relatively increased with increase in feed/inoculum ratio and temperature. Anaerobic digestion can occur in the mesophilic as well as in the thermophilic range. Agitation speed of 30 to 70 rpm enhances cumulative biogas yield in the range of 5.3 to 31.3% as well as the biomethane content in the range of 4.3 to 26.1% in comparison with biomethanization without agitation. Agitation speed above 30 rpm gradually decreases the cumulative biogas yield and its biomethane content. Modified Gompertz and Exponential Rise to Maximum kinetic growth models can be used to simulate cumulative biogas/biomethane production from the biomethanization of cattle manure, pig manure and chicken manure mixture co-digested with pineapple fruit waste (co-substrates) and content of chicken-gizzard. Biomethanization of cattle manure, pig manure and chicken manure mixture co-digested with pineapple fruit waste (co-substrates) and content of chicken-gizzard is thermodynamically feasible, spontaneous and endothermic in nature. The activation energy (E) of the biomethanization process was found to be 3.324 kJ/mol, indicating the endothermic nature of the biomethanization process. The negative values of (ΔG0 ) and positive value of (ΔH0 ) suggest that at higher temperature or thermophilic temperature (50 – 60°C) hydrogenotrophs might be predominant in the biodigester and perhaps could mostly be responsible for the biomethane generation through the hydrogenotrophic methanogenesis pathway than through the acetoclastic methanogenesis pathway. The specific heat capacity at constant volume and constant pressure, specific internal energy and specific enthalpy of the biogas and biomethane content increased with increase in temperature.
ETHICS APPROVAL AND CONSENT TO PARTICIPATE
Not applicable.
HUMAN AND ANIMAL RIGHTS
No Animals/Humans were used for studies that are base of this research.
CONSENT FOR PUBLICATION
Not applicable.
CONFLICT OF INTEREST
The authors confirm that the content of this article has no conflict of interest.
ACKNOWLEDGEMENTS
The authors would like to thank the technical staff of the Central Research Laboratory of Ladoke Akintola University of Technology, Ogbomoso for the access, help, support and use of the laboratory facilities